电磁设计效率低、成本高,传统方法为何难破局?
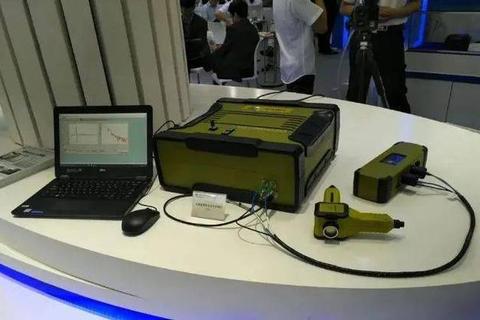
在5G通信、卫星导航、智能汽车等领域,电磁器件的性能直接决定产品竞争力。传统的“理论计算-手工建模-实验室验证”设计流程,常因精度不足、周期漫长、成本高昂等问题备受诟病。例如某通信企业设计一款毫米波天线时,因电磁耦合效应预测偏差,导致三次样机迭代失败,直接损失超500万元。面对这样的行业痛点,HFSS仿真软件赋能高效精准电磁设计创新突破,正成为工程师破解复杂电磁难题的核心工具。
高频电路板设计如何突破传统瓶颈?
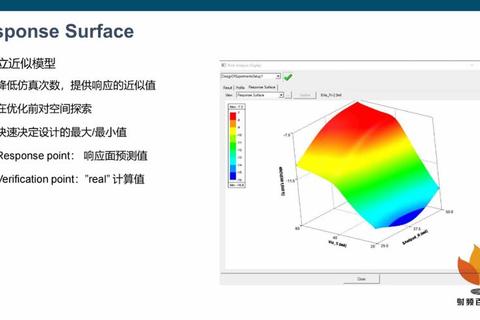
高频电路板设计中,信号完整性和电磁兼容性是最难平衡的指标。传统方法依赖经验公式,但面对5G毫米波频段的多层板设计,寄生参数和辐射干扰的复杂性使人工计算几乎失效。
HFSS通过参数化建模与自动化扫描技术,实现了设计效率的跃升。例如某企业设计WiFi 6E天线时,利用HFSS的宽频带自适应网格技术,仅用3天完成从2.4GHz到7.2GHz的全频段仿真,将反射系数(S11)优化至-30dB以下。其核心在于:
1. 智能网格剖分:根据电场强度自动加密关键区域网格,相比人工调整效率提升5倍;
2. 参数化优化:通过变量驱动模型,同步调整微带线宽度、介质厚度等12个参数,找到最优解组合;
3. 多方案验证:在虚拟环境中模拟10种接地结构,筛选出辐射效率最高的方案,实测误差小于0.5dB。
多物理场耦合难题如何破解?
当电磁器件遭遇高温、振动等复杂工况时,单一物理场仿真难以反映真实性能。某卫星通信设备因未考虑热变形对天线相位的影响,导致在轨运行时波束指向偏移2.3°,通信速率下降40%。
HFSS的创新突破在于双向电热耦合仿真。以某环形器设计为例:
在电磁仿真中导入材料温变参数,自动计算导体损耗(焦耳热达15W/m²);
通过Icepak热仿真模块,预测器件在85℃环境下的温度梯度分布;
将热形变数据反馈至电磁模型,修正后的相位一致性误差控制在0.1°以内。
这种跨物理场协同仿真,使设计容差从±5%压缩至±1%,同时减少50%的物理样机测试次数。
复杂系统设计怎样实现精准仿真?
相控阵天线、车载毫米波雷达等复杂系统涉及数千个组件耦合,传统仿真软件常因计算资源不足被迫简化模型。某汽车厂商在77GHz雷达设计中,曾因忽略PCB板与外壳的互耦效应,导致虚警率超标。
HFSS通过混合算法与分布式计算,突破了大尺度仿真的技术极限:
3D组件复用技术:将天线单元网格保存为独立模块,在整机仿真时直接调用,计算时间从72小时缩短至8小时;
区域分解法:将车载天线阵列分割为32个子域并行计算,内存占用降低60%;
AI辅助优化:基于历史数据训练神经网络模型,自动推荐馈电位置和匹配网络参数,使某MIMO天线设计迭代次数从20次减少至5次。
从工具升级到方法革新:工程师的进阶指南
HFSS仿真软件赋能高效精准电磁设计创新突破的本质,是将经验驱动转变为数据驱动的研发模式。对于企业而言,建议分三步构建竞争力:
1. 版本选择:优先采用2022 R1及以上版本,其集成的3D组件库和AI优化模块可提升30%仿真效率;
2. 能力建设:参考《HFSS微带天线仿真设计保姆级教程》等资源,掌握参数化建模、多物理场耦合等核心技能;
3. 流程重构:建立“仿真-测试-数据库”闭环,例如某研究所将500组天线仿真数据导入知识库,使新项目开发周期缩短40%。
电磁设计的未来属于那些善用工具、敢于创新的团队。当传统方法遭遇天花板时,HFSS仿真软件赋能高效精准电磁设计创新突破,正为行业开辟一条“虚拟验证、一次成功”的新路径。
相关文章:
文章已关闭评论!